 | | |
Задача 1.
Повышение производительности бумагоделательных машин достигается увеличением их скорости. Однако простое увеличение скорости машин без конструктивных изменений обезвоживающих элементов сеточной части и технологического режима обезвоживания и формования бумажного полотна приводит к резкому ухудшению качества бумаги. Происходит это вследствие резкой интенсификации процесса обезвоживания полотна на сетке машины и преимущественной в связи с этим ориентации волокон в направлении скорости фильтрации, т.е. перпендикулярно плоскости листа.
Для устранения этого технического противоречия (производительность - качество) была предложена принципиально новая схема формования бумажного полотна напылением, реализуемая на машине типа "Кивач". Основное достоинство этой схемы: процессы обезвоживания и формования бумажного полотна разделяются и, следовательно, исключается влияние резкой интенсификации обезвоживания на качество формования. На рис. 1 показано, как масса из напускного устройства 1 подается в клин между сеткой 2 и отжимным валом 3, обезвоживается и в виде факела 5 со сбрасывающего вала напыляется на подвижный экран (сетку) 6 прессованной части.
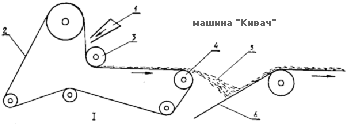
Такая схема позволила резко (в 5 раз) увеличить производительность машины без ухудшения качества формуемого бумажного полотна.
Наряду с многочисленными достоинствами нового способа формования бумажного полотна обнаружился один существенный недостаток. Вследствие того, что бумажная масса представляет собой полидисперсную систему (волокна различных размеров), а также оттого, что адгезия волокон разных размеров к сетке различна, в факеле напыляемой массы наблюдалась сепарация (фракционирование) волокон. При этом в верхней части факела сосредоточивались крупные и длинные волокна, в нижней - мелкие. Это, в свою очередь приводит к разносторонности формуемого листа - к градации волокон по толщине листа (рис. II).
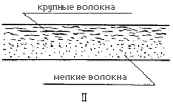
Правда, и на обычных бумагоделательных машинах имеется такая разносторонность, но там она менее явно выражена. Причина в том, что в начальный период обезвоживания массы на сетке мелкие волокна проваливаются в ее ячейки до тех пор, пока не образуется фильтрующий слой из более крупных волокон. При этом получается следующая градация волокон на толщине листа (рис.III).
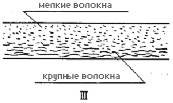
Итак, задача - избежать нежелательной разносторонности полотна (хотя бы в рамках, регламентируемых соответствующими ГОСТами на бумагу).
Решение задачи не было найдено ни на стадии проектирования, ни на стадии экспериментальных исследований нового способа формования, и при защите проекта на научно-техническом совете головного института отрасли (НИИЦМАШ) на этот недостаток было указано как на самый существенный, могущий опорочить многочисленные достоинства нового способа при выработке массовых видов бумаг. В связи с этим необходимо отметить, что существует целый ряд бумаг (обойные, кабельные и пр.), к котором предъявляются противоположные требования - здесь нужна разносторонность.
В дальнейшем при решении этой задачи решено было использовать АРИЗ.
Первая стадия алгоритма - это выбор задачи и, более конкретно, - рассмотрение следующих вопросов:
Какова техническая цель решения задачи? очевидно, в нашем случае - устранить сепарацию, так нам тогда казалось.
Какие характеристики объема заведомо нельзя менять при решении задачи? Во-первых, - сам принцип раздельного обезвоживания и формования (не только из-за чувства авторского самолюбия, но и из-за многочисленных достоинств метода; во-вторых, - при производительность машины (т.е. скорость).
Проверяем, можно ли достичь той же цели решением "обходной" задачи. Задача должна иметь принципиальное решение. "Обходная" - это более общая задача: либо отказаться от принципа напыления и получится обычная плоскосеточная машина, либо найти другой способ.
Далее АРИЗ-68 рекомендует сравнить первоначальную задачу с тенденциями развития данной отрасли техники. Но аналога нет, т.е. нет машин, работающих на данном принципе.
Сравнение же "обходной" задачи с тенденциями данной отрасли техники приводит нас к применению способов, могущих уменьшить разносторонность. Это, во-первых, увеличение процентного содержания более однородной фракции - целлюлозы до 100% (кстати, высококачественные сорта бумаг вырабатываются именно из 100%-ной целлюлозы). Во-вторых - замедление обезвоживания в первоначальной стадии, в начале сеточного стола - в результате интенсивная тряска, снижение скорости машины, мокрые отсасывающие ящики, желобчатые регистровые валики, гидропланки, которые снижают промой волокна и, следовательно, разносторонность.
В-третьих, более тщательный размол, преследующий своей целью выравнивание фракционного состава бумажной массы перед отливом. Многие зарубежные фирмы (Швеции, Англии, Японии) интенсивно работают над созданием промышленных фракционаторов волокна. Фракционирование, т.е. разделение волокон по размерам (фракциям), дает возможность использовать при выработке отдельных видов бумаг волокна одной фракции и тем самым компенсировать разносторонность.
В-четвертых, зарубежные фирмы широко используют двухсеточные машины, в которых бумажное полотно обезвоживается между двумя сетками. Это - "Инверформ", "Вертиформа", "Паприформер", "Бел-Байформер", "Аркуформа" и т.п. Скорость фильтрации в них уменьшается вдвое, т.к. при той же производительности процесса обезвоживания фильтрация идет через две сетки. При этом на каждой из сеток откладывается, как уже рассматривалось, слой крупных волокон, препятствующих провалу мелких (рис. IV)
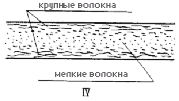
В-пятых, применяются ровнители. Ровнитель - это цилиндр, обтянутый точно такой же сеткой, что и основная сетка на машине. Механизм действия его аналогичен рассмотренному для двухсеточных машин. Зарубежные фирмы придают ровнителям первостепенное значение несмотря на то, что они сложны в изготовлении и капризны в эксплуатации.
Далее в АРИЗ рекомендуется сравнить прямую и "обходную" задачи с тенденциями развития ведущей отрасли техники.
Хотя в нашем случае трудно определить, какую же отрасль техники считать ведущей по отношению к целлюлозно-бумажной промышленности, мы нашли простой выход - искали аналоги везде, где можно. Аналогичные устройства имеются в теплоэнергетике. Это так называемые ПМЗ - пневмомеханические загрузчики угля в топки мощных котлов.
Механический загрузчик разбрасывает уголь ровным слоем по цепному поду топки. Так как крупные куски угля летят дальше, факел пламени в топке неоднороден. С целью равномерной загрузки угля по крупности по всему поду печи применяется поддув - при этом струя воздуха подхватывает мелкие куски угля и угольную пыль и транспортирует их равномерно с крупными (рис. V)
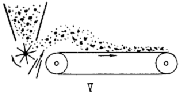
В нашем случае такое решение не подходило по той причине, что мы не представляли себе возможных последствий поддува и неизбежных в связи с этим искажений факела, а следовательно, и профиля (поперечного) бумажного полотна.
Сопоставление первоначальной и "обходной" задач предопределяет выбор - первоначальная задача проще и экономичнее.
Определяем требуемые количественные показатели (скорость, производительность, качество, габариты) и вносим в них поправку на время, т.е. учитываем, что от момента нахождения решения и до создания новой машины или приспособления, позволяющего решить задачу, вышеперечисленные показатели могут возрасти.
Уточняем требования, вызванные конкретными условиями, в которых предполагается реализация изобретения, в частности, учитываем тот факт, что экспериментальная установка уже создана и установлена на Кондопожском целлюлозно-бумажном комбинате и поэтому решение должно касаться незначительных конструктивных изменений.
Вторая стадия АРИЗ - уточнение условий задачи. АРИЗ рекомендует уточнить задачу, используя патентную литературу, - аналогов, к сожалению, в отрасли не оказалось. Просматривать же все другие патенты при современной их классификации не представлялось возможным из-за недостатка времени. Рекомендуется также ответить на вопрос: можно ли решить данную задачу, если не считаться с затратами - своеобразное снятие тормозов с побочных решений, могущих привести к требуемому результату. Ответ: "обходную" - можно, первоначальную - нет.
Как изменится задача, если уменьшить величину требуемого показателя почти до нуля (производительность). В этом случае можно, например, предложить ручной отлив: масса наливается на сита и встряхивается. Раньше так и делали. В настоящее время ручной отлив не применяется. Это для "обходной" задачи. На нашей схеме при V=0 (нулевой скорости) не будет напыления. При очень же большой скорости факел выродится в плоскость, полотно. В этом случае, казалось бы, задача решена. Однако остается неблагоприятная ориентация волокон в поперечном направлении к плоскости листа, связанная с резким обезвоживанием на отжимном валу.
Третья стадия - аналитическая.
- Определить идеальный конечный результат (ИКР), т.е. ответить на вопрос: что желательно получить самом идеальном случае? Очевидно, было - внизу мелкая фракция, стало - равномерная градация по толщине листа.
- Определить, что мешает получению ИКР, т.е. ответить на вопрос: в чем состоит помеха? Ответ, очевидно, будет: в сепарации.
- Определить, почему мешает, т.е. ответить на вопрос: в чем непосредственная причина помехи? Ответ: центробежные силы, различная адгезия волокон в зависимости от размеров и физической массы.
- Определить, при каких условиях ничто не мешало бы получить идеальный конечный результат, т.е. ответить на вопрос: при каких условиях помеха исчезает?
А. Можно ли сделать так, чтобы помеха исчезла? Нельзя, так как без действия центробежных сил не будет напыления;
Б. Можно ли сделать так, чтобы помеха осталась, но перестала быть вредной? Можно, если сделать факел напыляемой массы симметричным. Каким образом? Может быть, регулировать радиус сбрасывающего вала? В этом случае мы меняем угол раскрытия факела. Чем меньше радиус, тем меньше угол раскрытия факела. В частности, при радиусе, равном нулю, сепарация исчезает.
Кстати, ИКР должен быть иным, чем мы его ранее представляли. Действительно, гораздо лучше иметь в центре толщины полотна грубые и длинные волокна - несущий скелет листа, обеспечивающий необходимые физико -механические качества бумаги полотна, а по обеим сторонам - мелкие волокна, придающие хорошие потребительские свойства.
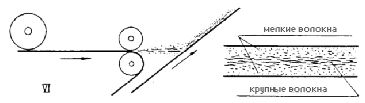
На этом этапе задача решается. В самом деле, для достижения ИКР - симметрии распределения волокон по толщине полотна достаточно сделать симметрический факел. Это достигается постановкой дополнительного верхнего сбрасывающего вала, обтянутого сеткой (рис. VI).
Это решение неявным образом существовало на этапе выбора задачи (вспомним ровнитель). Но ранее сработала, на наш взгляд, инерция - коль скоро наша машина не плоскосеточная, то и метод производства другой, и функции, выполняемые в данном случае сбрасывающим валом и ровнителем, разные. Ровнитель подтягивает волокна, а сбрасывает вал изменяет всю картину факела. Поэтому на такой стадии правильное решение прийти не могло.
В дальнейшем было решено поставить верхнюю сетку - из конструктивных соображений, а также в связи с там, что при малых скоростях обезвоживающий вал брал на себя массу.
Как видим, алгоритм не только позволит решить задачу, но и решить ее более качественно, чем мы могли ожидать. "Вредный" эффект сепарации перестал быть вредным и, наоборот, позволил получить такой эффект, который невозможен на обычных бумагоделательных машинах, "благополучных" с точки зрения сепарации.
В данном случае решение этой задачи пришло на аналитической стадии алгоритма. Но мы продолжили решение задачи дальше с целью нахождения возможно большего числа вариантов. Следующая стадия использования алгоритма и наиболее эффективная - оперативная.
Устанавливаем с учетом решений на предыдущих стадиях техническое противоречие (ТП) типа "форма" (схема машины) - "вредные факторы" и находим с помощью таблицы типовых приемов возможность установления ТП - это приемы №1, 33, 21, 22.
1 - принцип дробления. Он уже использовался при разделении процессов обезвоживания и формования бумажного полотна, преследуя в принципе те же цели. Вспомним, что в противоречие вступили "форма" машины (схема - плоскосеточная) - "вредные факторы", ухудшающие качество формуемого бумажного полотна.
33 - прием гласит: объекты, взаимодействующие с данным объектом, должны быть сделаны из того же материала. В самом деле, на факел мы воздействовали другим факелом, совместив их по плоскости раздела в один.
21 - принцип проскока. Вредные или опасные стадии процесса должны преодолевать на большой скорости. И это было - факел на большой скорости превращается в плоскость.
22 - принцип "обратить вред в пользу". Он и был использован при решении задачи.
Создается обманчивое впечатление, что три предыдущих стадии решения по АРИЗ не давали решения и только четвертая стадия - оперативная давала каскад принципов, в зашифрованном или почти в явном виде содержащих решение. Что ж, мы тоже пытались это сделать, а именно: использовать таблицу типовых приемов устранения технических противоречий, минуя первые три стадии АРИЗа и не тратя времени на очистку ее (задачи) от шелухи внешних атрибутов. И - ничего не получилось.
Прежде чем приступить к решение задачи оперативным путем, необходимо четко выявить условие задачи, найти ИКР и ТП. В противном случае можно до бесконечности манипулировать таблицей, используя лишь кажущиеся ТП (вспомним хотя бы, как мы неправильно определили ИКР). И наоборот, используя первоначальные стадии АРИЗ, можно прийти к решению гораздо раньше.
Имея уже приемлемое решение, мы несколько раз применяли АРИЗ с учетом этого решения, чтобы отыскать возможно больше побочных вариантов. И здесь пришло еще одно очень интересное прикладное применение рассмотренного выше способа устранения сепарации при производстве бумажного полотна методом напыления. Мы уже отмечали, что чем меньше радиус сбрасывающего вала, тем меньше угол раскрытия факела, и наоборот. А в нашем случае, когда сбрасывающих валов два? Оказывается, что симметрия факела в этом случае нарушается, т.е., изменяя радиус сбрасывающих валов, мы можем регулировать положение крупной фракции по толщине листа, располагая ее ближе то к одной, то к другой стороне листа. Значение этого решения трудно переоценить. Существует целый класс бумаг с покрытием: хром-эрзац, клеевые ленты, кабельные бумаги, мешочные бумаги с ламинированным слоем - одним из существующих недостатков которых является скручиваемость. Тот же недостаток существовал и при эффекте сепарации. В малой степени он выражен во всех бумагах, т.к. эффект сепарации в них не изжит (на этом основано, кстати, определение машинной и свободной сторон листа).
Регулируя структуру листа по толщине, мы можем, следовательно, менять характеристики скручиваемости. Наносим, например, клеевой слой на ленту для склеивания шпона (в мебельной промышленности) и, чтобы избежать скручиваемости, загоняем на противоположную сторону листа мелкую фракцию волокон - моменты от усадки компенсируются.
|